In today’s competitive market, it is more important than ever for companies to have precision-machined parts.
Precision grinding is an important process in manufacturing. It helps to create parts with tight tolerances and a high degree of accuracy. This process is used in various industries, such as automotive, aerospace, and medical, resulting in many precision machining suppliers. These suppliers have the necessary equipment and expertise to get the job done right. They can help to improve the quality of a company’s products and increase their efficiency.
What Is Precision Grinding?
Precision grinding is an abrasive machining process that produces very fine finishes or makes very small cuts, using an abrasive wheel as the cutting tool. The term “precision” grinding can be applied to any type of surface finish operation that results in a precise, smooth surface. A precision ground surface has a very low level of irregularities and is typically produced by removing only a small amount of material from the workpiece.
Precision grinding is an important step in the manufacturing process of many products. It can help improve the surface finish, dimensional tolerances, and mechanical properties of parts. It can also be used to prepare surfaces for other manufacturing processes, such as heat treatment or coating.
Precision grinding is generally used to produce high-quality finishes on hardened materials and to create very tight tolerances. It can be used to produce surfaces with extremely high levels of flatness and parallelism, as well as to create very thin cross sections. It can also be used to produce optical quality finishes.
Types Of Precision Grinding
There are several types of precision grinding, including surface grinding, cylindrical grinding, and centerless grinding. Each type has its own benefits and applications. For example, surface grinding can produce very flat surfaces with high levels of accuracy. Cylindrical grinding can create parts with complex shapes and tight tolerances. And centerless grinding is often used to create round parts with no axial orientation (such as bearings).
1. Surface Grinding
Surface grinding is a type of grinding process that uses a spinning abrasive wheel to remove material from a workpiece surface. Common applications include grinding flat surfaces, shaping tools, and removing Gates and burrs.
The technology can be used on materials including ferrous and non-ferrous metals, glass, ceramics, plastics, and composite materials.
Surface grinding is typically used as a finishing operation after another machining process such as turning or milling. Because it leaves a smooth surface finish with minimal tolerances, surface grinding is often used in the manufacturing of precision parts and components.
There are two types of surface grinders: horizontal spindle and vertical spindle. Horizontal spindle grinders have the wheel mounted on a horizontal axis, and vertical spindle grinders have the wheel mounted on a vertical axis. The majority of surface grinders use the horizontal spindle configuration.Workpieces are held in place on the worktable with a chuck or magnet. The spinning grinding wheel then removes material from the workpiece surface until it reaches the desired shape or size.
2. Cylindrical Grinding
Cylindrical grinding is the process of grinding the outside surfaces of a cylinder. These surfaces may be straight, as in the case of a rod or pipe, or contoured, as in the case of a shaft or crankshaft.
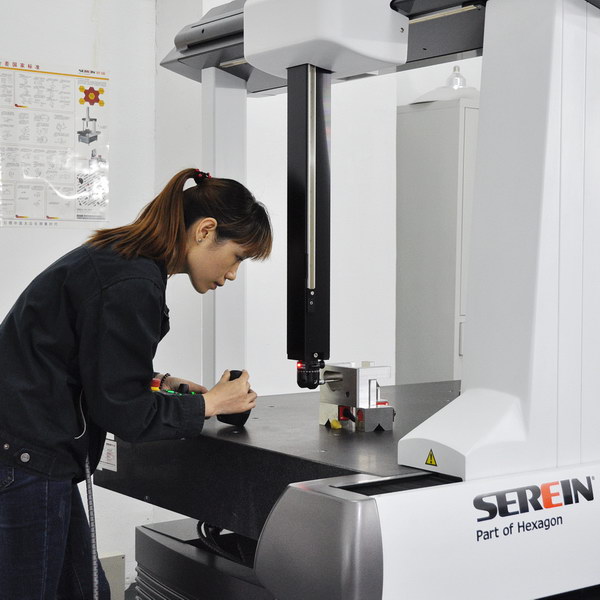
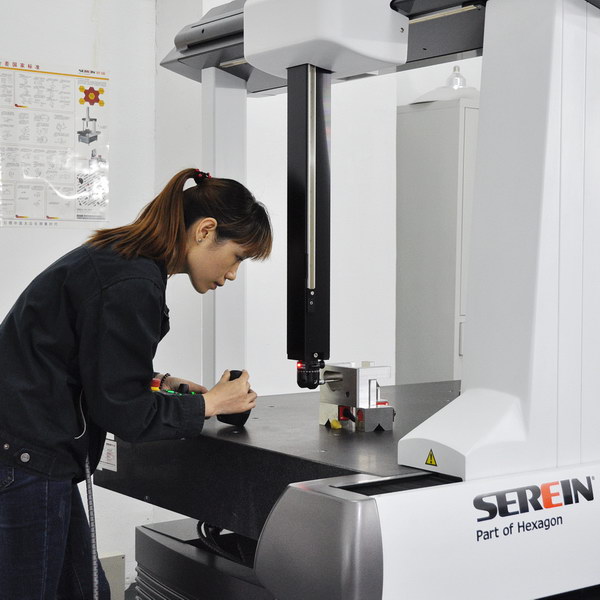
Cylindrical grinding is usually done by mounting the workpiece in a chuck and rotating it while the abrasive wheel is moved across its surface. This can be done manually, using hand-held tools, or by machine. Cylindrical grinding can also produce a very smooth finish on the workpiece.
There are several types of cylindrical grinders. The most common type is the universal cylindrical grinder, which can be used to grind workpieces of almost any shape. Other types include the centerless grinder, which is used to grind workpieces with very tight tolerances, and the internal grinder, which is used to grind the inside surfaces of cylinders.
Cylindrical grinding is a very versatile process and can be used to produce a wide variety of parts. Some of the industries that use cylindrical grinding include automotive, aerospace, and medical.
3. Centerless Grinding
Centerless grinding is a machining process that uses abrasive cutting to remove material from a workpiece. Centerless grinding differs from centered grinding operations in that no spindle or fixture is used to locate and secure the workpiece; the workpiece is secured between two rotary grinding wheels, and the speed of their rotation relative to each other determines the rate at which material is removed from the workpiece.
Centerless grinding is typically used in preference to other grinding processes for operations where many parts must be processed in a short amount of time.The centerless grinding process is versatile and can be used on a variety of materials.
However, it has some limitations when compared to other machining processes. For example, centerless grinding cannot be used to create a very precise finish on a workpiece, and it is not well-suited for machining materials that are hard or brittle. Centerless grinding also tends to produce a greater amount of waste material than other types of grinding processes. Despite these limitations, centerless grinding is a very effective machining process and can be used to achieve precise results on a variety of workpieces.
Which Parts Need Precision Grinding?
Some common examples of parts that need precision grinding include:
-Gears
-Pins
-Shafts
-Valves
-Surgical instruments
-Aircraft components
Precision grinding can be performed on many different materials, including metals, plastics, and ceramics.
The type of material being worked on will determine which type of precision grinding tool should be used. For example, diamond grinding wheels are often used to grind hard materials, while softer materials can be ground with alumina or silicon carbide wheels.
The type of finish desired will also dictate the type of precision grinding tool used. A rough finish may be achieved with a coarse-grained wheel, while a finer finish requires a more abrasive wheel.
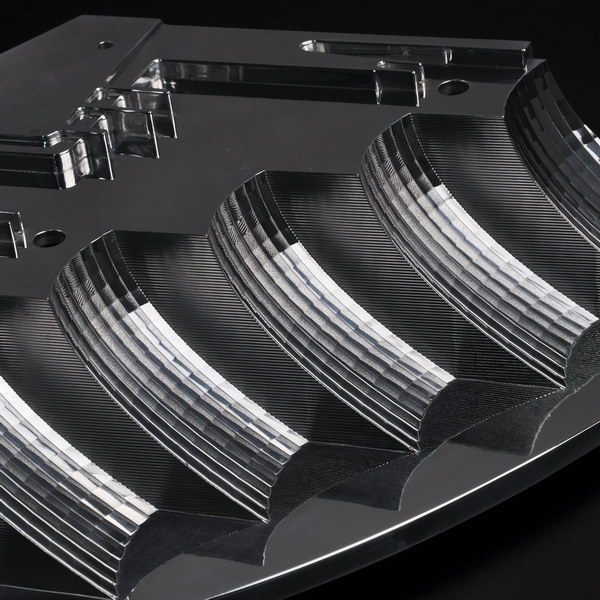
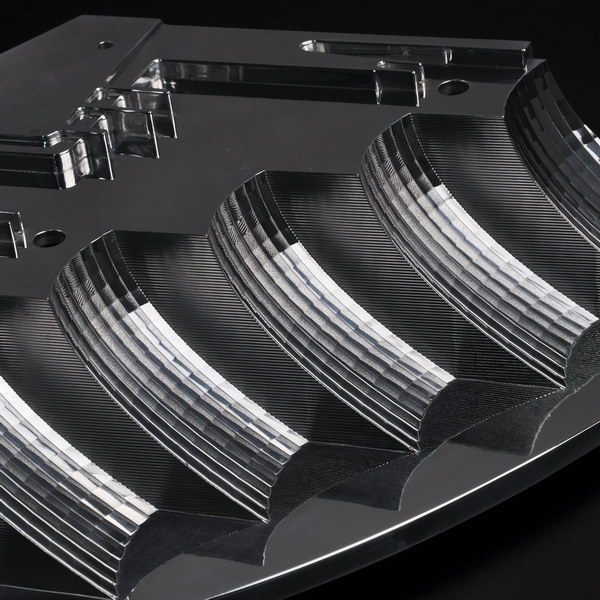
When choosing a precision grinding tool, it is important to consider the material being worked on, the desired finish, and the tolerance requirements. Precision grinding is a critical step in many manufacturing processes, so it is important to select the right tool for the job.
Conclusion
Precision grinding is an important step in manufacturing. It ensures that materials are cut correctly and accurately, which is crucial to the overall quality of the final product. Without precision grinding, products would not meet the high standards that consumers expect. In addition, precision grinding helps to prolong the life of tools and machinery by preventing wear and tear. Precision grinding is an essential part of the manufacturing process, and it is important to choose a reputable company that has experience in this field.


Must See
-
Entertainment
/ 2 days agoFaveSzn’s Revelation: Dating Choirmaster at 10 and Sexual Curiosity
Nigerian singer, Chidozie Ugochinyere, popularly known as FaveSzn, has revealed that she once dated...
By Flying Eze -
Europe
/ 2 days agoWhy Hungarian Prime Minister Orban visited
Two months later, the leaders of China and Hungary met again. Hungarian Prime Minister...
By Flying Eze -
News
/ 2 days agoThree dead and millions without power as Tropical Storm Beryl hits Texas
Man, 53, and woman, 74, killed by fallen trees and third person drowns amid...
By Flying Eze